Operation Contract (OC)
The purpose of Contract Packaging is to relieve the customer from day-to-day Operational Packing of their end products. Our responsibilities are extensive but not limited to equipment handling, supplying, and training of manpower as well as supply of packaging consumables. We offer Contract Packaging Services that adhere to a wide variety of customizable pack styles preferred by the customers. This enables customers to focus on core activities, whilst at the same time benefiting from process simplification, single point of contact, and zero packaging inventories.
Advantages
- Single Point Responsibility.
- No inventory of consumables and Spares.
- Delivery of the product in manufactured condition to the end-user.
- Elimination of pilferage.
- Cost effective operation and maintenance.
- Reliable time management to meet dispatch schedules.
Some of the on-site operation and Maintenance Service contracts for packaging equipment are mentioned below:
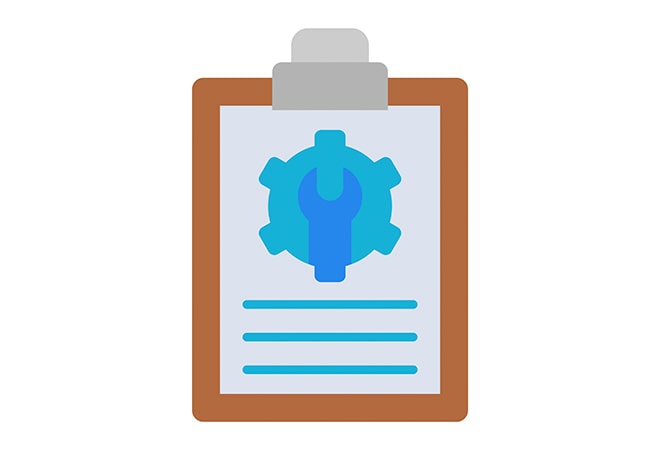
Annual Maintenance Contract (AMC)
This program is designed to keep your equipment running at maximum efficiency to minimize the costly and unexpected interruptions and downtime that may result from an unexpected equipment problem.
- We undertake an annual maintenance contract for our products with minimum operating cost. Our engineers make periodic visits to the customer’s place to take up preventive maintenance of precise tools & equipment to avoid sudden breakdowns during peak load period. For our AMC customers we keep all the necessary spares at any given time. Customer's requirements would be fulfilled as top priority.
- As a special case we will undertake AMC for other supplier products on request.
- Non-AMC customers will be offered the best service on a call basis.
Field Engineering (FE)
With over two decades of experience in the development of packaging systems for Indian industry, GSTPL can help you implement efficient, economical methods of packaging, handling, and shipping your products.
WE SEE THE BIG PICTURE
When we meet with a new customer, the first thing we do is perform an audit of their current process. Our technicians spend time in the facility to assess what the exact product is; what type of equipment is being used and what condition that equipment is in; where the product is being shipped; what the shipping and packaging expectations are; and what the current conditions of the process are. Is there damaged freight, are there customer complaints, or is the facility experiencing frequently repeated issues?
We are often able to identify the root cause of existing issues or present an optimized process that will improve efficiency and ultimately save money for our customer.
FOCUS ON PROBLEM SOLVING
Our problem-solving process relies on an open minded, creative outlook. We may set up controlled test environments so that we can test and prove the efficacy of our solutions before any changes are implemented. The insight gained through the audit and testing process helps us work toward the best possible formula to match the equipment with the right film and materials.
Our working knowledge of your overall systems, equipment, and product together with our long-term investment in your success is what makes us your ideal partner in roll wrap applications.
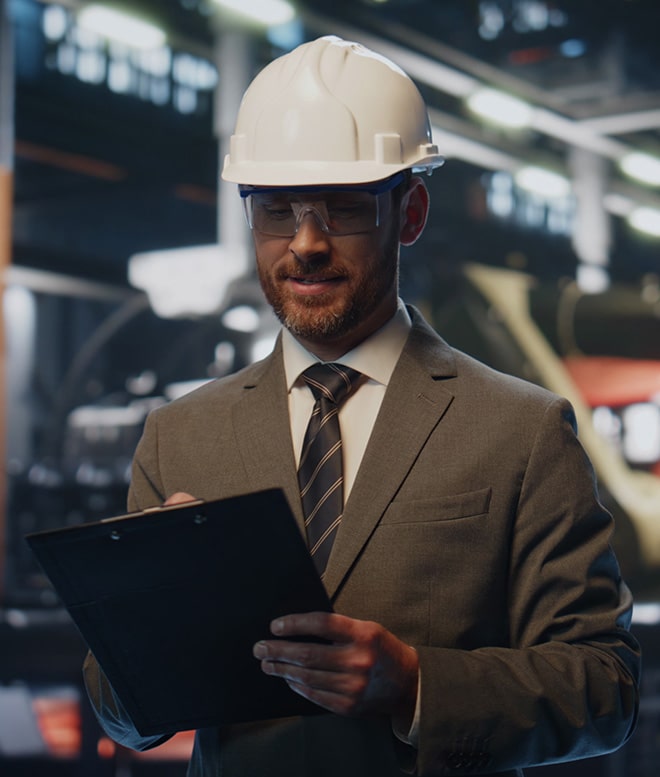